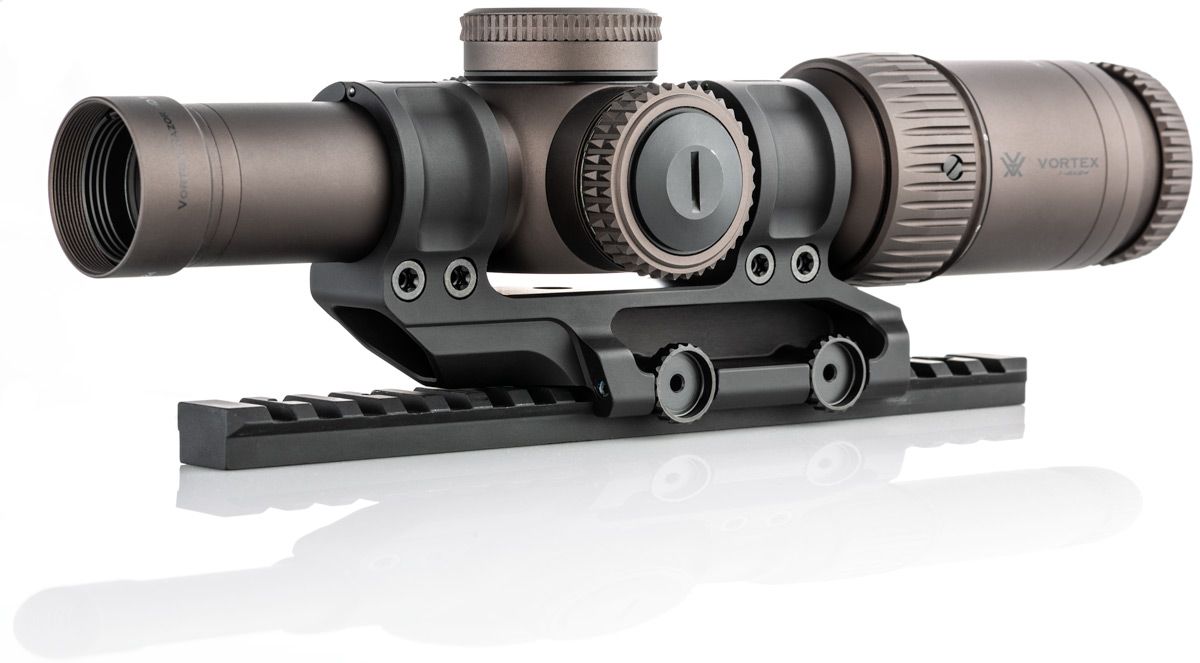
Quality optic mounts like the quick-detatch Scalarworks LEAP are a critical, but sometimes overlooked component of a proper AR build. To learn more about the thought process and hard work that goes into creating a high-end optic mount, we recently reached out to Scalarworks founder and owner, Phil Bartoszewicz.
If you missed our recent interview with Phil about his company’s revered Scalarworks Peak iron sights, you can read that article here.
Q: Phil, let’s start with your background and how the idea for the Scalarworks LEAP came about…
Phil Bartoszewicz – Scalarworks – My background is that I am an industrial designer by trade, and I got into firearms and shooting in around 2008. The first thing I got into was handguns, which I loved, but I have always enjoyed tinkering with things, and there’s really not much that you can do with pistols.
Because of that, I ended up building my first AR, and I was reasonably happy with everything surrounding the AR platform, except for one thing…the optic mounts.
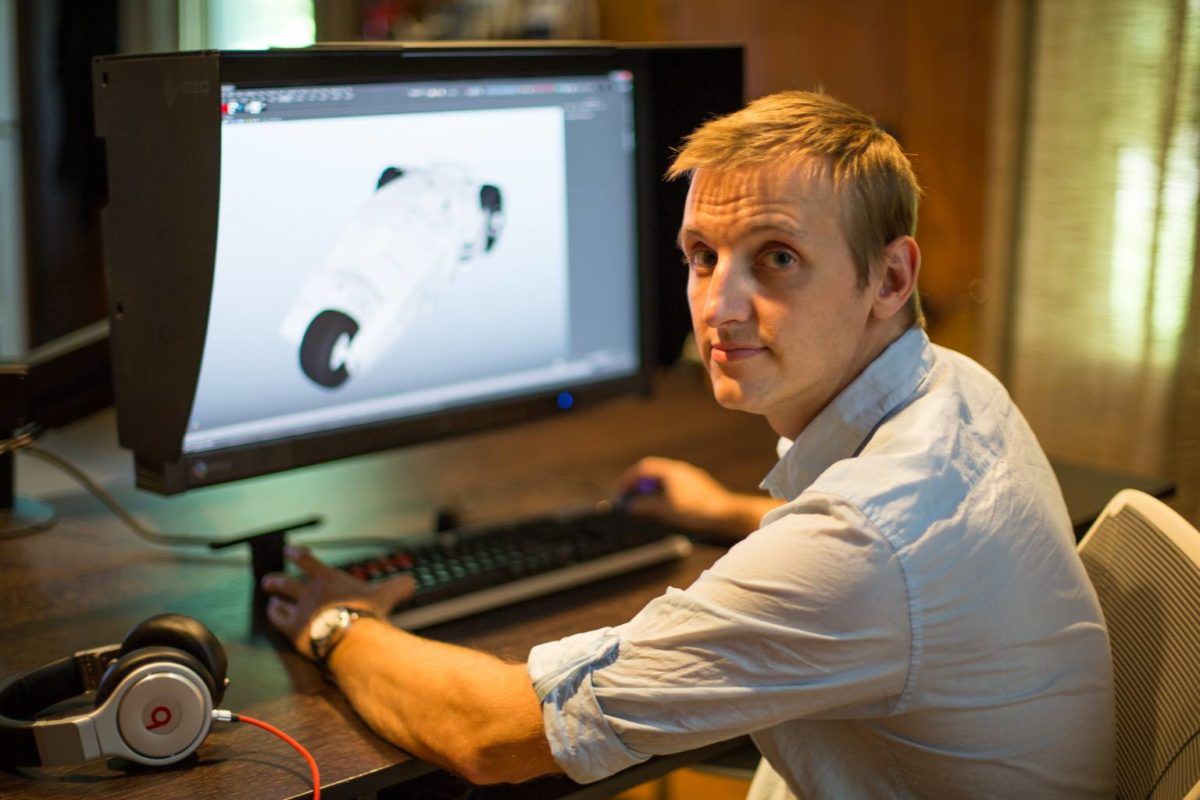
The first optic I bought was an Eotech, which was heavy and bulky, yet I somehow managed to break it as I was installing it. I then started looking into Aimpoints. I bought an Aimpoint T1 with a quick detach mount…but I soon found myself buying different mounts for it…I tried every one that was on the market at the time. To me, they all had issues.
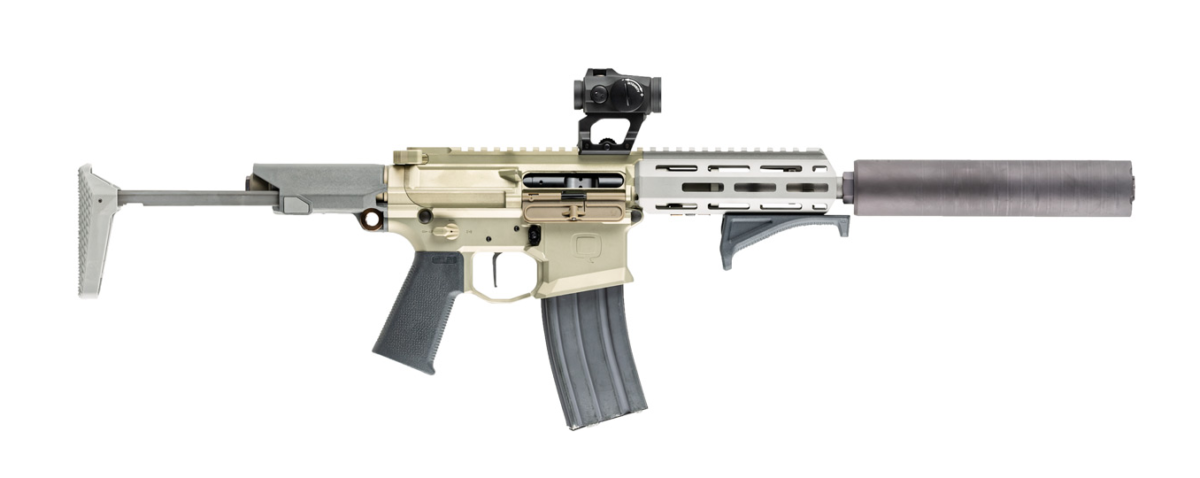
Q: What kinds of issues exactly?
Phil Bartoszewicz – Scalarworks – It didn’t make any sense that the mount should weigh more than the optic. It was just something that bothered me. I ended up going back and forth through a lot of mounts, and I knew that I did like quick-detach mounts. I liked being able to pack more guns into a single case, and be able to take the optic off, and be able to put it back on and have it return to zero was something that made a lot of sense.
Also, around this time, firearms training became more popular, as did MOLLE. I can recall being in a class, and realizing that optic mounts with levers that stuck out really bothered me. The levers would hang on gear, and always be in my way.
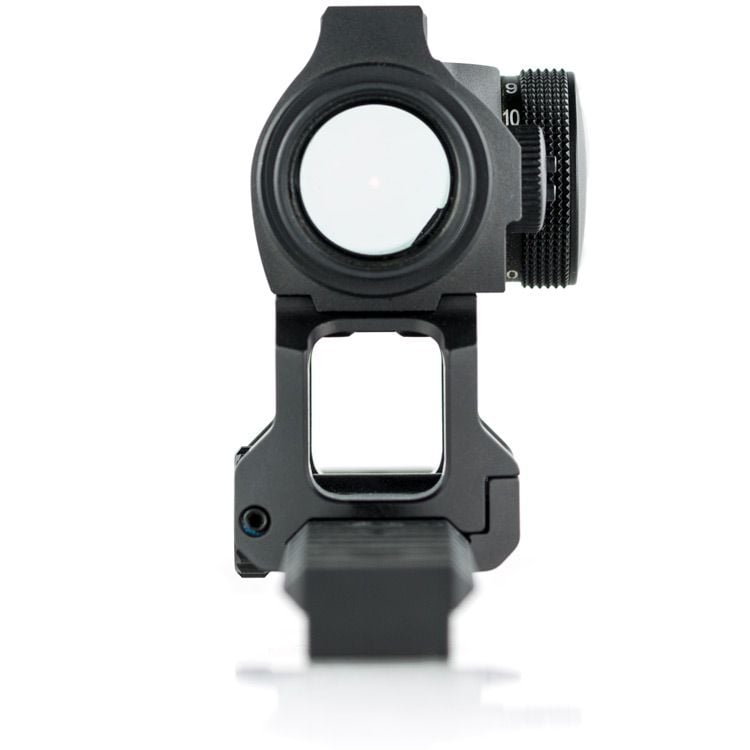
Q: So, when exactly did you decide to create something different?
Phil Bartoszewicz – Scalarworks – Well, I had access to Solidworks (design software) because of a job I had at the time, and I began tinkering with designs. I tinkered for a while, but nothing came of it, and I ended up leaving it alone.
Eventually though, there just came a time in my life where I decided to take a look at my ideas again. I took a leap, and got some of my savings together, and had a production mount done. I called it a “Low Drag Mount” at the time, and I made 100 of them.
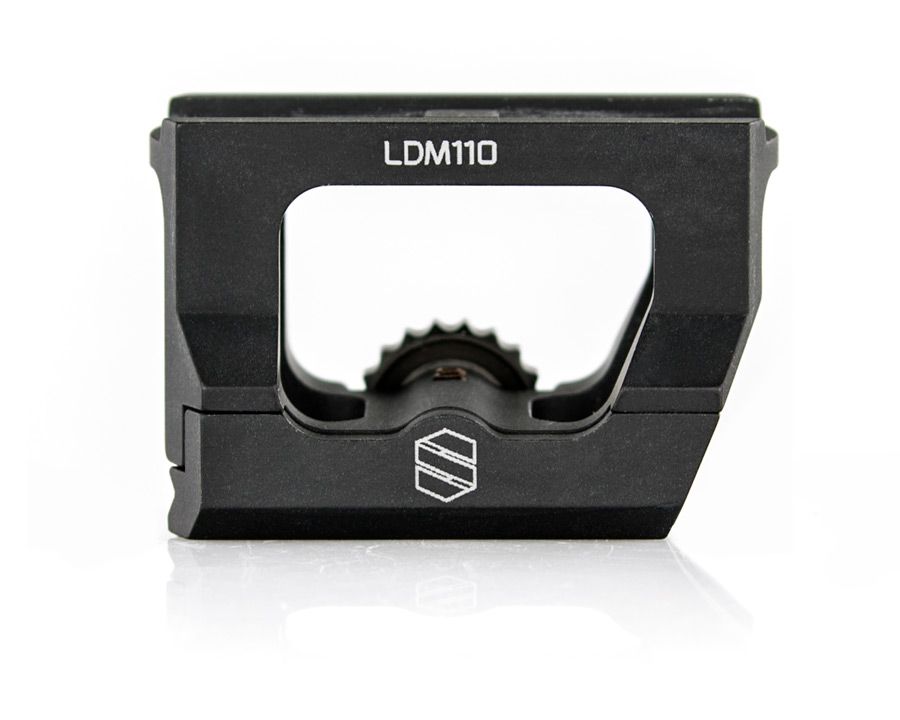
At this point, I really didn’t want to ask anyone’s permission on how or where to sell. I didn’t want to go to stores and ask people if they’d be willing to sell what I created. I decided to go direct, make a website, put out a press release…and the rest is history.
That first batch we did of Low Drag Mounts sold out in a week, and in that time Primary Arms reached out to me to be a dealer. I then realized I could do both – I could sell direct, and I could have dealers.
Q: How big is Scalarworks today?
Phil Bartoszewicz – Scalarworks – I started a dealer network, and today I have over 130 dealers, plus around 10 internationally. The company was started in New Jersey, where I live, and still do…but I moved the business to Pennsylvania because that made sense for a lot of reasons. It was just me for the first four years, but now I have five people working with me. We’re growing fast, and things are great.
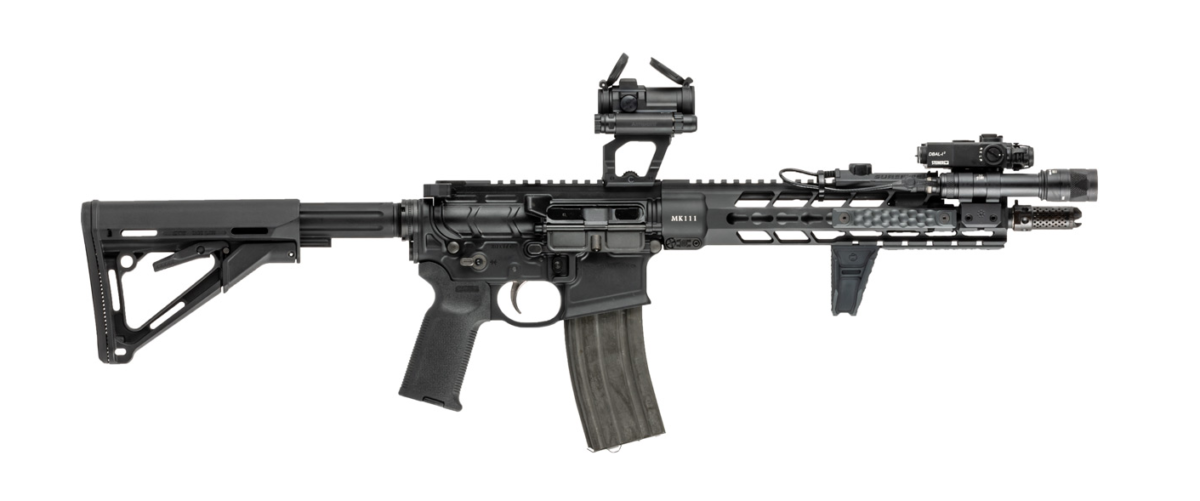
Q: How did the distinct look of the Scalarworks LEAP come about?
Phil Bartoszewicz – Scalarworks – I’m an industrial designer, and the crux of industrial design is that things can look good and also function well. It’s not one or the other. Just because something looks like crap does not mean it is any more reliable or better functioning than something that looks really nice.
Looking at the mounts that existed then, and the mounts that exist today, most are extremely basic. Frequently, it’s just a “box” underneath the optic. The optics themselves are pretty nice looking…Aimpoints, RMRs, MROs…they’re all really good looking optics. I’ve gotten to know some of the people at those companies who design those optics, and I know that they care about making things that function and look good. My approach with the Scalarworks LEAP is no different.
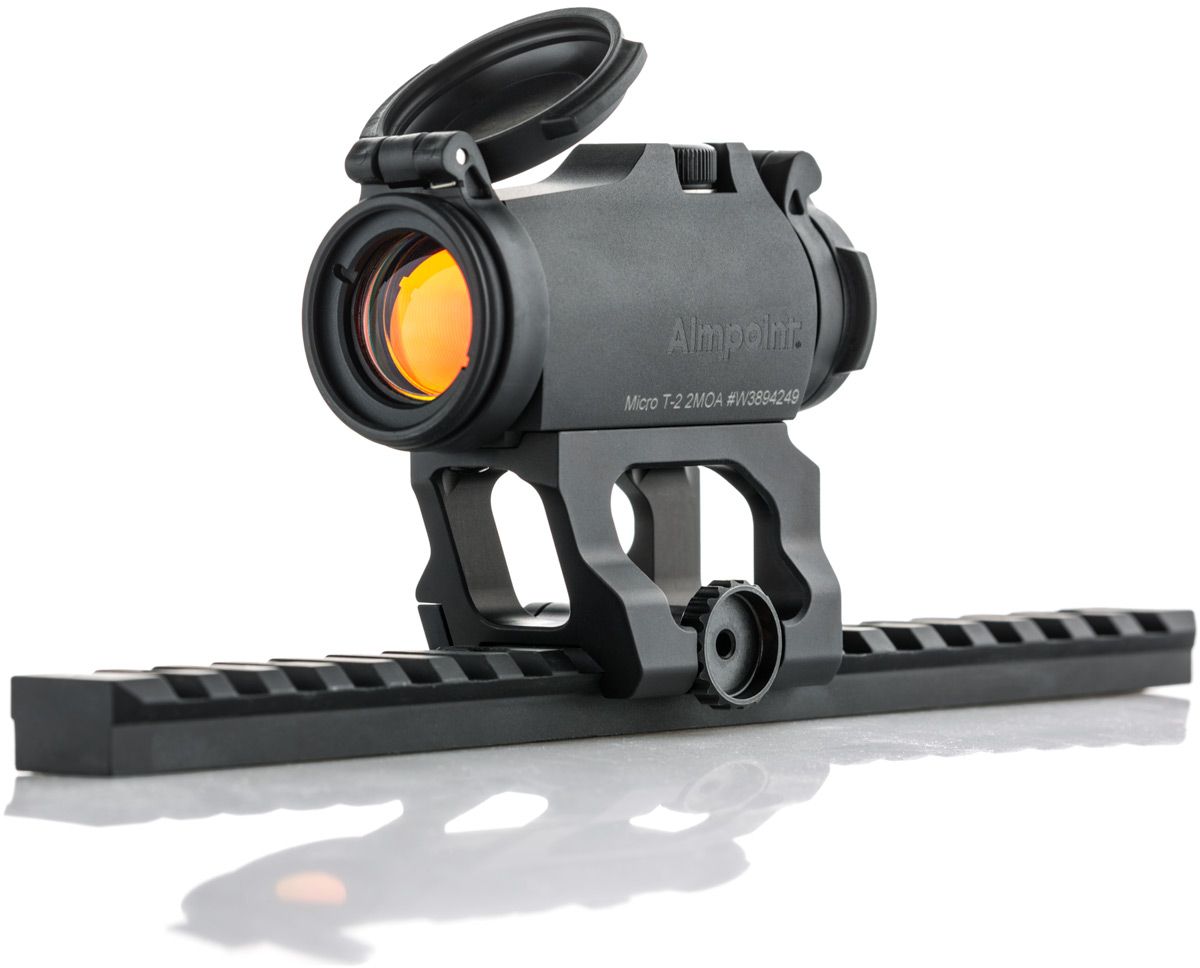
I’d also say that making my mounts look good gives me a competitive advantage. If everyone else is selling a box with a lever, if I could differentiate myself somehow, that would be beneficial.
The first version I did I thought looked pretty good. However, with additional time and resources, I’ve been able to do better. I think you can see that with today’s Scalarworks LEAP mount, which is about as sophisticated design as I can come up with. I’ve strained to get every gram out of it and put every feature I could get into it. It’s as about as good a mount I can make…at the moment.
Q: Do you find that your goals have changed over time as you’ve gotten more proficient?
Phil Bartoszewicz – Scalarworks – I’d say that’s accurate. When I first started, the bar for me was “as good,” as I didn’t quite know what I was doing in this space. I certainly was not a veteran mount designer. My desire was to make something that was as good strength and function-wise, but lighter and more compact.
Once I had achieved that, my aspirations grew. I started focusing on making mounts even more robust and lighter. I also thought that I could make something easier to use and better looking as well. Hopefully, I have achieved that, and so far, it seems that the meeting of form and function we are providing with the Scalarworks LEAP is working out pretty well for us.
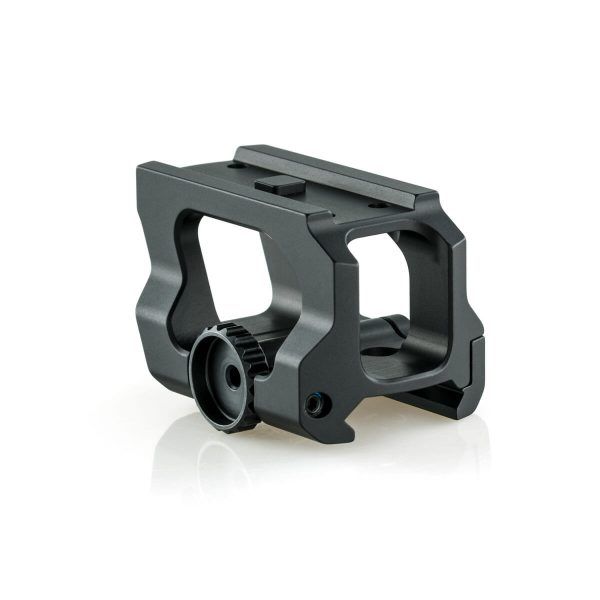
Q: Can you talk about the materials you use for the Scalarworks LEAP mounts?
Phil Bartoszewicz – Scalarworks – When I started, everyone was making their mounts out of 6061 T6, which is fine, but again, it’s the most common Aerospace alloy that machine shops had, so that’s what they picked. I tend to doubt they did any research, because if they did, they would have seen 7075 is a bit more expensive and harder on tooling to machine, but is way stronger, and it only weighs a small bit more than 6061.
As a way to differentiate myself and deliver a lightweight product, but have the same strength as everyone else (or better) I went to the best alloy I could get. To me, 7075 is the best bang for the buck, and it’s significantly better strength-to-weight than 6061.
While there are some fine mounts out there at a reasonable price, when it comes to being a pioneer with 7075, I believe in zigging when everyone else is zagging, if there is a good reason for it. In this case, using 7075 seemed like a way to be different, and be better, at the same time.
More than that, there was no one else making ultra-high-end mounts, and it seemed like an area where aiming for the high end would provide real-world performance gains and would allow us to achieve levels of strength-to-weight that no one else was coming close to.
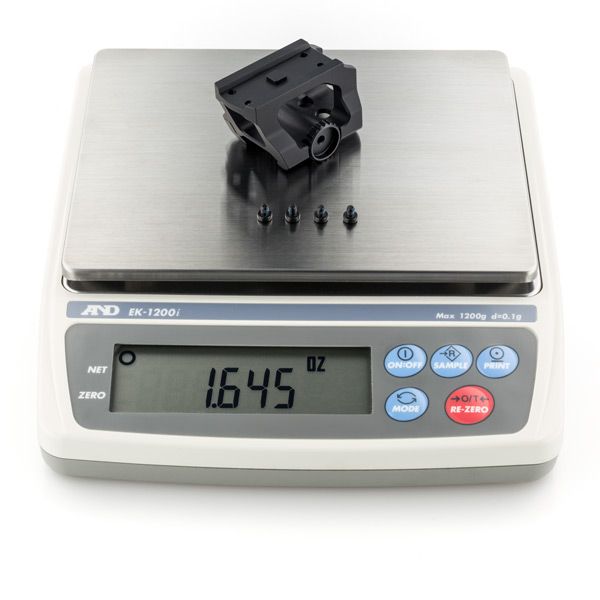
Q: Can you talk about the ClickDrive System on the Scalarworks LEAP and its benefits?
Phil Bartoszewicz – Scalarworks – I wish I could say I woke up one morning and had the idea, but it took a long time to get it to where it is now. My goal was something that didn’t have a lever. I liked the strength that a cross-bolt provided, but I wanted it to be quick-detach…something that you could just take off with your hands.
At first, I tried every kind of washer and anti-vibration loosening device that existed on the market. Nothing worked. Things would always end up vibrating loose…One day, I was looking at the design, and it all just fell into place. I was looking at the hunches that surround the wheel, and saw there was some space to work with.
I had designed the wheel so that it felt good in the hand and you could get traction on it, but I realized I could fit a ball in there. That would give me external force on the outside diameter, which would counteract the vibration loosening forces.
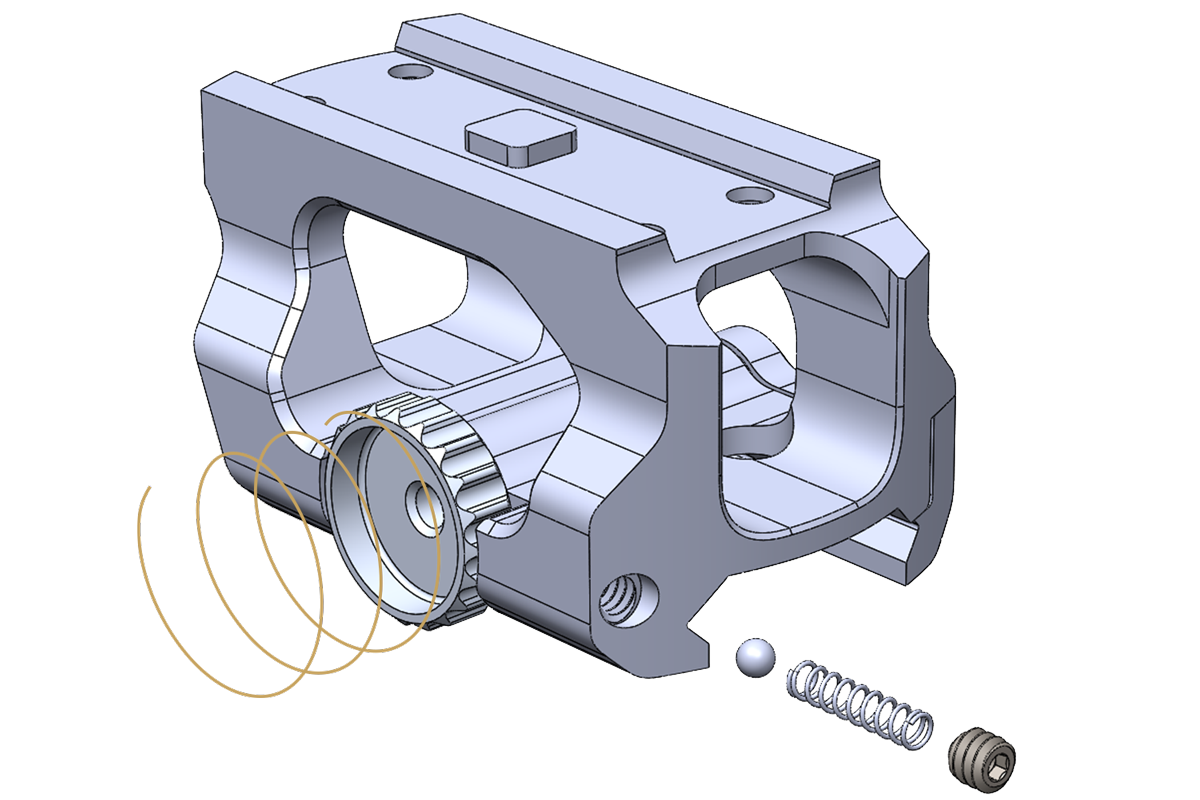
I did some further research on vibration loosening and learned that all I needed to do was add a force on the outside of the head of the screw that was superior to the vibration loosening forces.
These vibration loosening forces do not have a high peak, but rather have a cumulative effect. Basically, when the entire assembly vibrates, it’s loosening just enough for it to turn and then tighten back up…like a spring. That’s how a screw functions…it’s essentially a spring.
When you add torque to a spring, you are pre-loading it, and that pulls the two pieces together. What keeps it from vibrating loose is friction between the threads and between the head and the top plate of whatever you are trying to screw together. This is why so many bolt-on mounts require so much torque to not come loose.
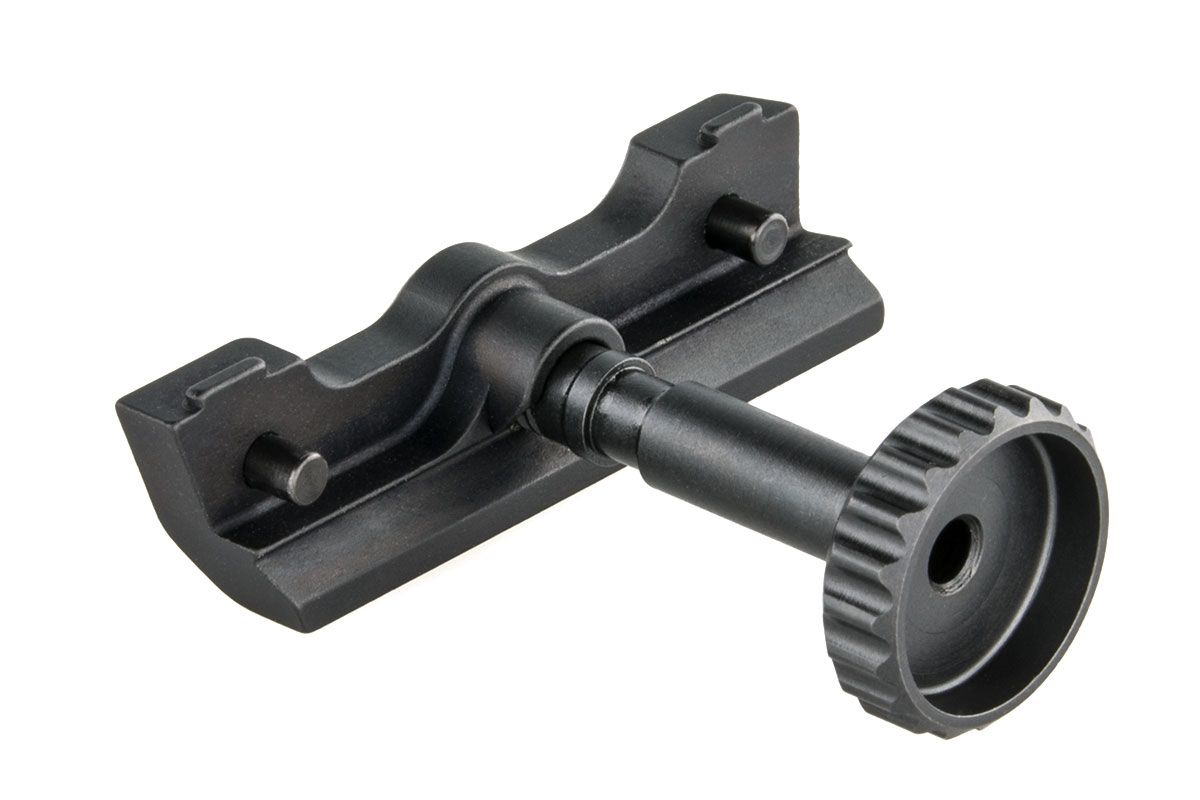
I discovered that if you design the mount properly, you don’t need large amounts of clamping force to keep a mount securely on a rail. The excessive amounts of torque many bolt-on mounts require is there purely to add enough friction in between threads and on the back of the head of the screw to keep the mount from vibrating loose. Basically, it’s so tight on there so that vibration forces won’t allow the spring to contract and vibrate free inside of the assembly…
Once I made the first prototype of the design I use today on the Scalarworks LEAP, it just worked. I shot 400-500 rounds, and it would not come loose. It was a eureka moment. That said, the concept was something that has been on a lot of Benelli and Mossberg shotguns for a long time, on the magazine tube of the Benelli M4, for example. The idea existed out there, it had just never been applied to a Picatinny mount.
Q: Can you talk about how the return to zero function works on the Scalarworks LEAP?
Phil Bartoszewicz – Scalarworks – The key to returning to zero is eliminating the degrees of freedom. I found that a lot of existing mounts had a sliding clamp. When you have that, you have a mount that can slide up and down, as well as back and forth. Early on, I decided the Scalarworks LEAP should not be able to move except telescopically on one axis, horizontally.
As you turn the screw on the LEAP, it moves the clamp in and out. As long as the screw cannot rotate, then there is no way for the clamp to move in any other direction than out. You end up with a substantial, resilient assembly. I kept evolving this idea, and now we have press-fit, hardened steel pins that provide three-points of contact that guarantee the mount has nowhere to go once it is tightened down.
Also, since your hand acts as the torque wrench, this guarantees the same torque each time. This is because your hand naturally has the same amount of strength each time you are applying the mount.
As long as the same person applies the mount to the gun, the wheel will stop at the same spot, every single time. If you use the maximum amount of torque that you can, it’s the same torque. To validate this, you can put a small witness mark on the side of the wheel, unscrew it, close your eyes, then screw it back on, you’ll see that it hits that mark every single time.
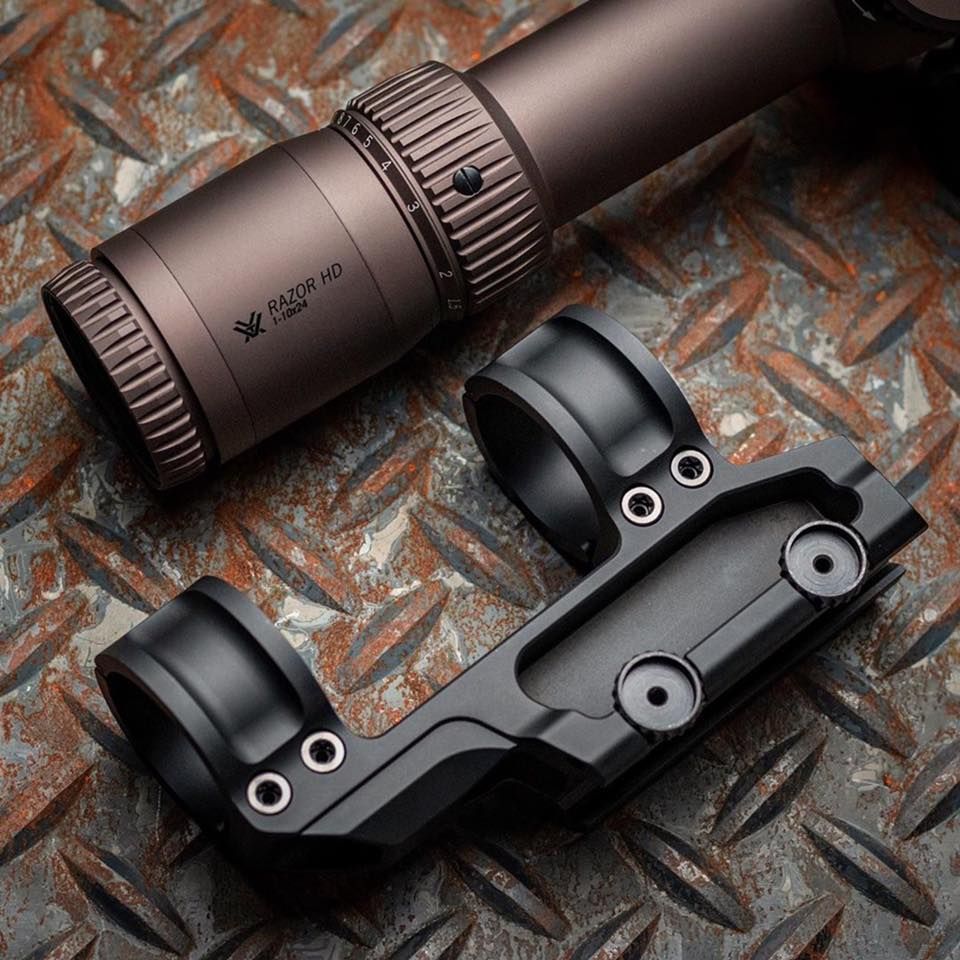
Q: With LPVOs becoming more popular, a lot of buyers are looking for mounts…can you walk us through the basics of what you’ve created for these optics?
Phil Bartoszewicz – Scalarworks – Before I made the Scalarworks LEAP Scope Mount, I had the idea simply for a ring that was completely round, and didn’t have any ears on it like traditional split rings do. The reason for that was just that it looked better, was a lower profile, and you could see your turrets no matter the configuration.
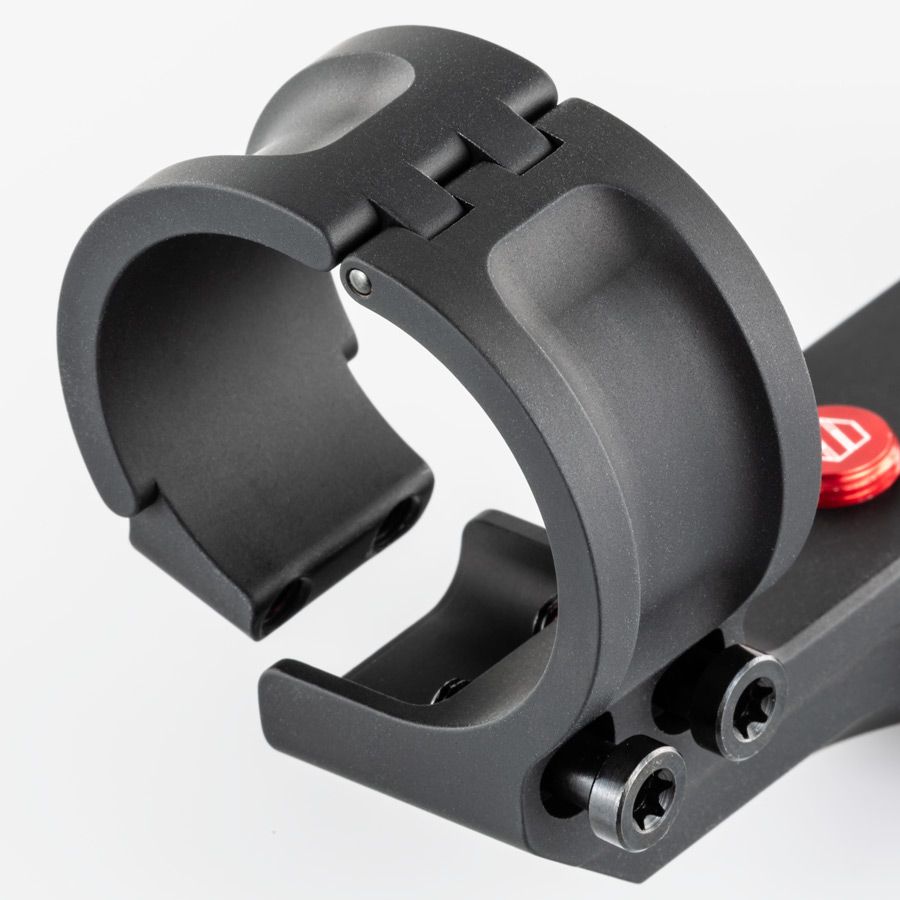
What you end up with is lighter, low profile, and easier to set up. By only having two screws and a hinge, you also don’t have to worry about the gap on one side being different than the gap on the other side. It gets rid of that completely.
Q: Was designing a scope mount a more intense endeavor than previous entries in the LEAP lineup?
Phil Bartoszewicz – Scalarworks – I was cautious, as to me, scope mounts are the absolute epitome of optics mounts—That’s where the stakes are the highest. You’re putting an expensive magnified optic onto a costly gun that is going to shooting out to ridiculous distances. If I was going to do a scope mount, I needed to take the time to do it right.
Our prototype and test for this was our Pro Mount, which has a single ring. I thought that if I could design the ring the way that I wanted, validate that it worked, then I could be reasonably certain the rings would work on a scope mount.
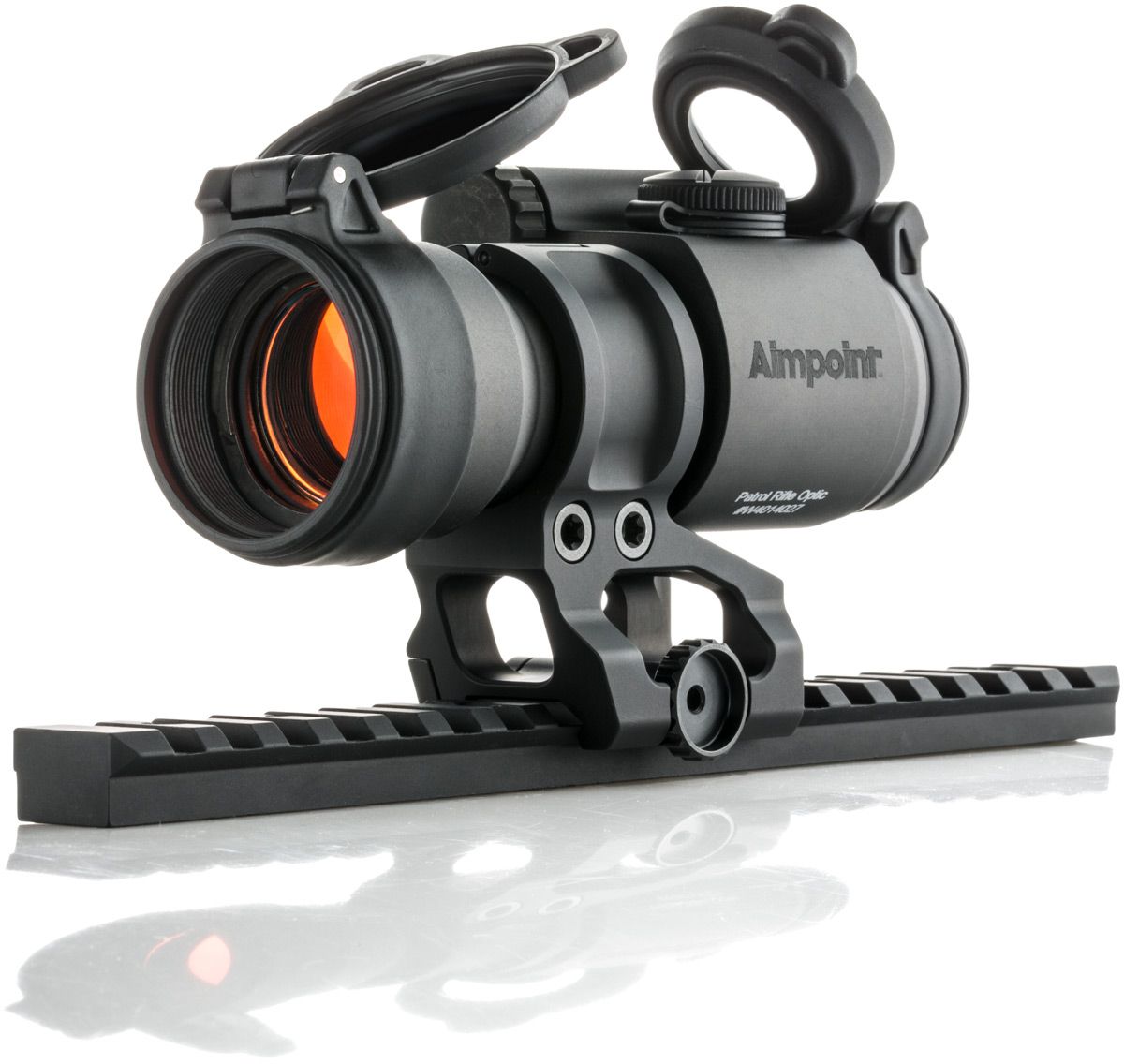
The Pro Mount came out and was a big success…and it led me to start working on the Scalarworks LEAP Scope Mount in earnest. I knew I wanted to have all of the features the other LEAP mounts had so that I could call it a LEAP mount as well.The final product has two thumbscrews, and we doubled the number of pins to help with side impact strength. I also wanted the mount to be as wide and as tall as it could possibly be. That’s how you maximize rigidity.
Q: Why was maximizing rigidity necessary?
Phil Bartoszewicz – Scalarworks – You want your entire gun to be as rigid as it can be for precision shooting. I felt the Scalarworks LEAP Scope Mount was no different. So, I ended up adding a lot of expensive and complicated features to the design of the base to achieve that.
I added an I-beam structure in the back…I also added torsional rigidity in the front by machining a tubular structure…Doing this adds a lot of extra machining expense, but it’s the kind of thing we can do better than others because we don’t own our own machines. We have a manufacturing partner who machines this stuff for us. I consider that a strength.
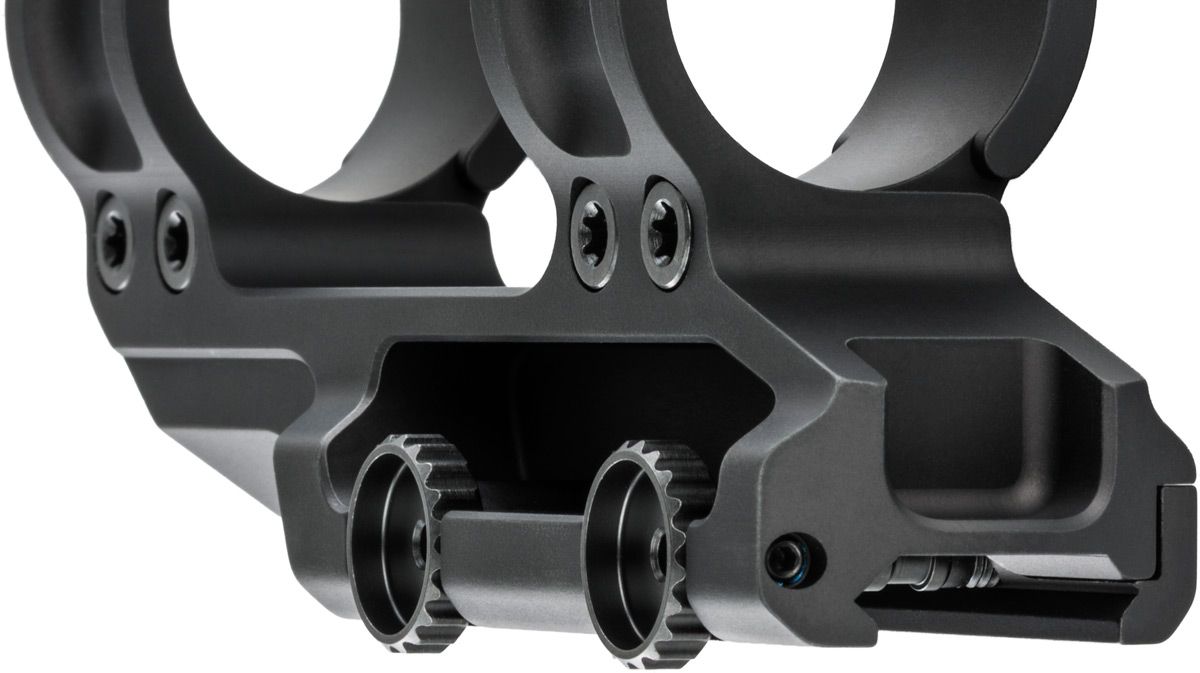
Q: Can you explain how that is a strength?
Phil Bartoszewicz – Scalarworks – I consider it a strength because when I am designing something, I am not thinking about “how many mills I have that are not being used at 100 percent capacity. What tooling do I have available? How big is the carousel? How many tools does it hold so I have to limit my operation? How many set-ups do I need to do?”
These are things that I am aware of, but I am not thinking about them when I am designing something for machining. Rather, I only am thinking about creating the absolute best design. How it’s made is really a secondary consideration.
In terms of cost, I understand that not everyone out there can afford a $400 scope mount, but there’s tons of people who can, and I felt those people were underserved with what was out there at the time, and maybe still are.
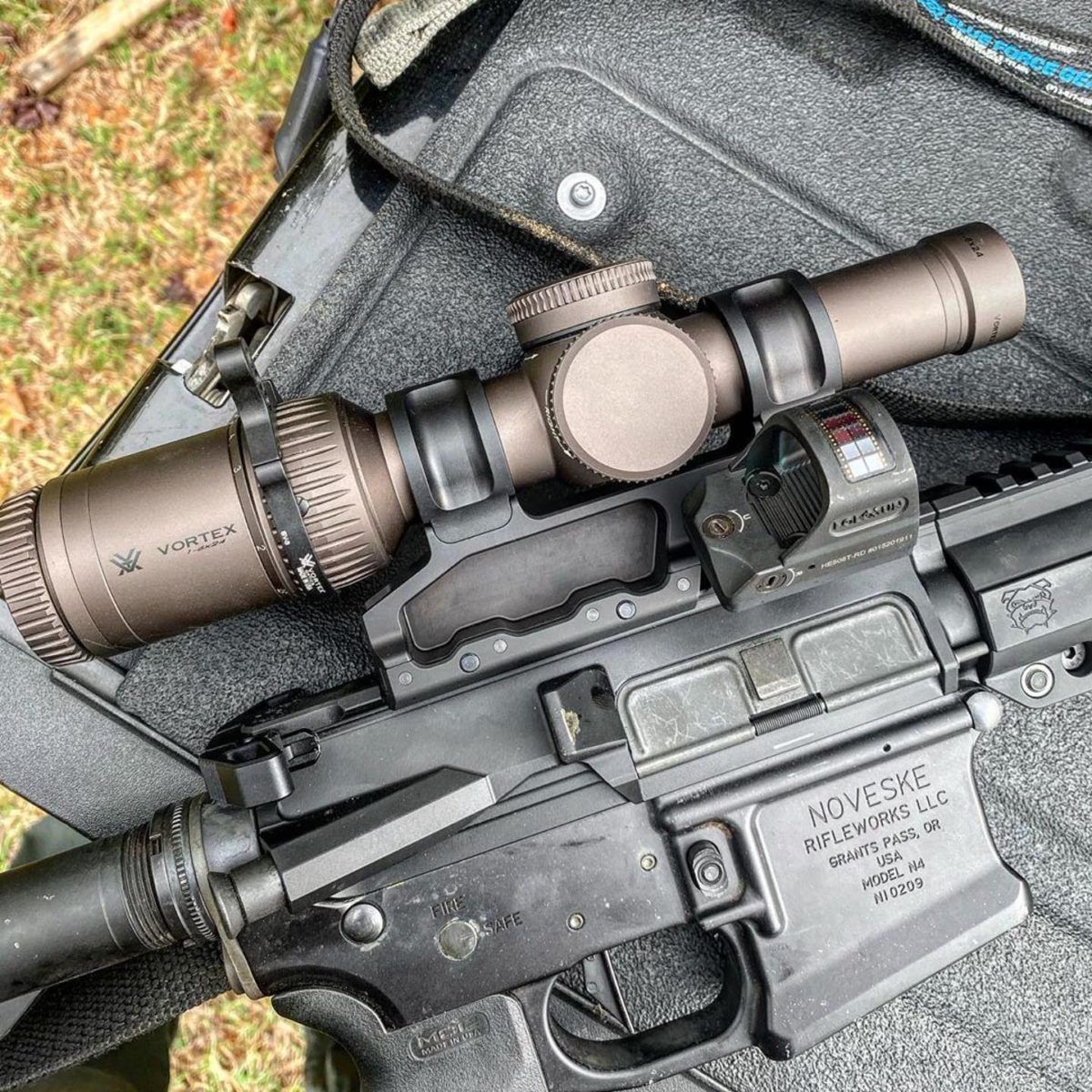
Q: Can you explain the LevelDrive feature offered on the Scalarworks LEAP Scope Mount?
Phil Bartoszewicz – Scalarworks – That was something that came in really late. It came about from my manufacturing partner telling me that Scalarworks LEAP Scope Mounts had come back from anodizing, and because of the complicated, perpendicular pockets that we have in it to lighten it in the right spots, we could not drain the anodizing fluid from it properly. We were told we needed holes in there for the fluid to drain out so that bubbles wouldn’t form.
At that moment, I had a realization that “what if instead of making a small hole, we make a big hole, thread it, and put a set screw with a flat top in there, and use it to level the flat base of the scope?” That was another legit eureka moment. They made a prototype, we tried it, and it worked exactly like I thought it would. I then patented it, and now we are the only ones that have it. It’s good for us, but it’s good for everyone.
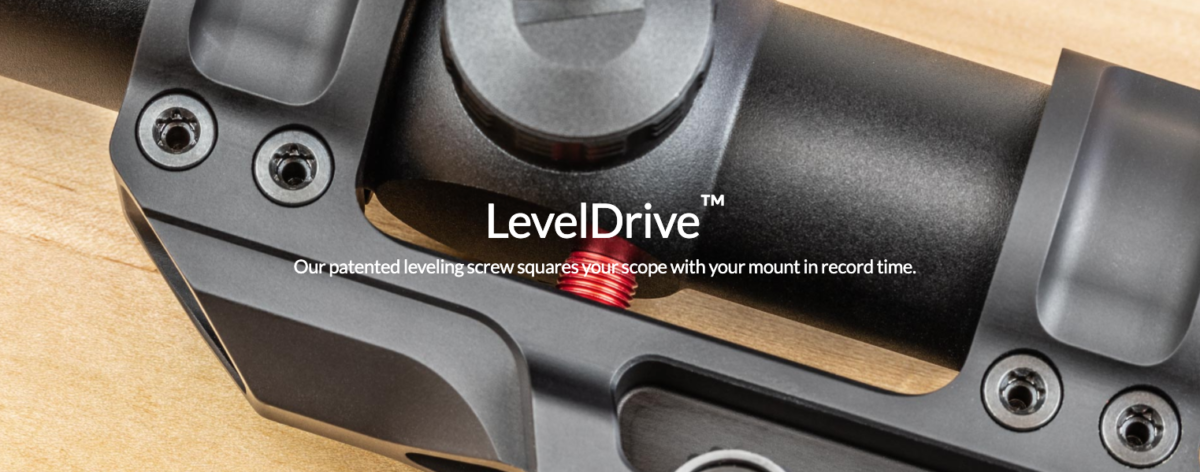
I think before LevelDrive, setting up a scope in a mount was awful for a lot of shooters. It took forever, and you were not 100 percent sure of your results unless you had a lot of sophisticated equipment to do the measuring and figure it all out. Now, anyone can level their optic in two or three minutes. It’s just a lot easier to set up. It’s great for people who are experienced, and for those who are not experienced, who would otherwise need assistance.
###
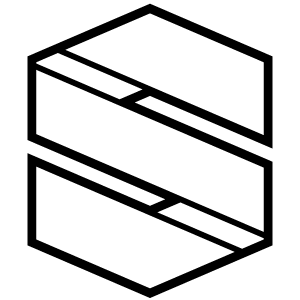